Human–robot interaction:
What changes in the workplace?
Research report
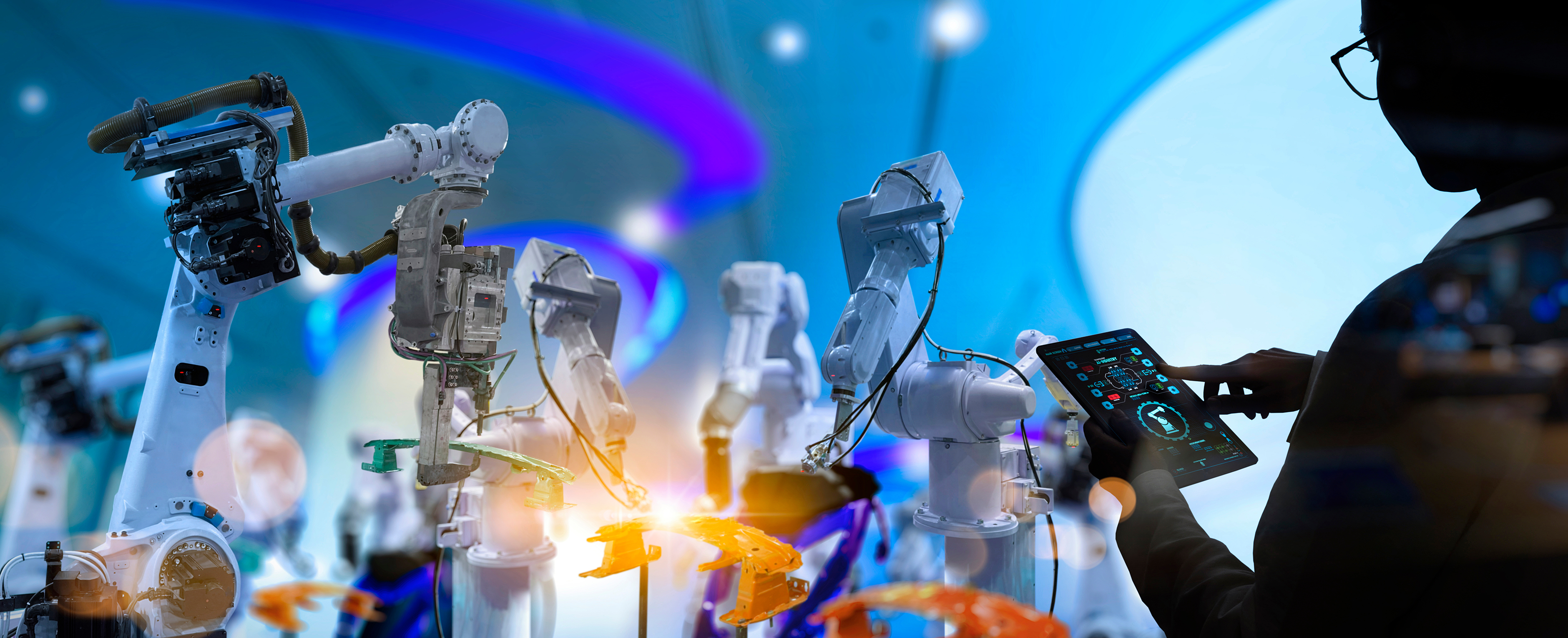
A new era of human–robot interaction
Advanced robotic systems and applications disrupt workplaces; they transform the way work is carried out, often resulting in changes to business models and redefining roles, tasks and methods of work. Artificial intelligence (AI) has played a pivotal role in enhancing these systems, giving them greater capabilities, functionalities and flexibility than more conventional robots. AI has also facilitated seamless collaboration and interaction between humans and robots in various industries. This is most prominently illustrated by collaborative robotic applications, through which AI enables closer worker–robot interaction in shared workspaces.
As advanced robots become more complex and prevalent in modern work environments, understanding how workers and robots interact and the implications for work organisation and working conditions is crucial for robots’ successful integration into the workplace. The changes brought about by autonomous or semiautonomous advanced robotics require thoughtful consideration and proactive management to ensure a positive impact on businesses and workers.
Drawing on survey data and case studies investigating advanced robotic systems and applications for task automation, this report highlights new forms of interaction between workers and robots and the changes to work organisation and working conditions that they entail. Read the highlights below and download the full report: Human–robot interaction: What changes in the workplace?
Key messages
The use of robots is becoming more concentrated: while fewer companies are using robots, the number of robots per company is increasing. Amid labour supply challenges stemming from demographic ageing, demand for robots is expected to increase.
Motivations for introducing robotics shape design choices and technology implementation. Using robots primarily to improve productivity may be a missed opportunity for more meaningful human–robot collaboration.
Robots are not causing widespread job losses, as some may have feared: the impact of automation on employment has been more nuanced, currently leading to more changes in job profiles than cuts.
While the use of robots has been driven mostly by the need to ensure high-precision outputs and safety at work, truly effective human–robot interaction requires a stronger focus on job quality, underpinned by the active involvement of workers affected.
Automation can result in productivity growth which should lead to the creation of good-quality jobs. The positive outcomes of automation should be equitably shared with workers.
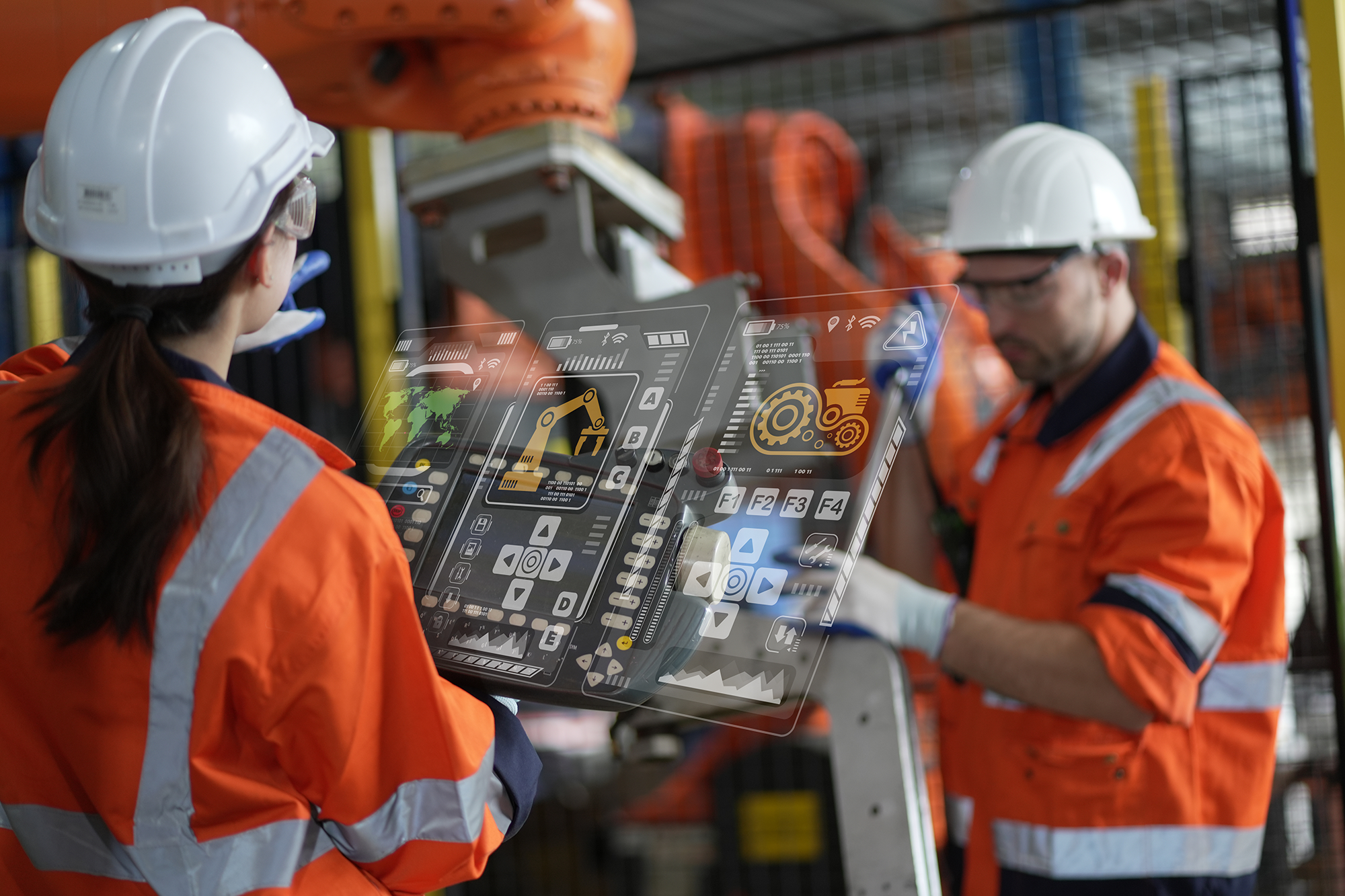
Chapter 1
Prevalence of robots and impacts on working conditions
Summary
Since 2018, there has been a slight decline in the number of enterprises utilising robots in the EU, while the number of robot installations has increased. This suggests that the EU’s robot market is becoming increasingly concentrated.
Given the high capital investment requirements and the economies of scale necessary to make investments in robots profitable, large enterprises dominate the market for robots in the EU. Around 1 in 5 large enterprises in the EU use industrial robots, while only 1 in 10 use service robots.
In general, the prevalence of service robots, capable of executing more complex tasks than industrial robots with a certain degree of autonomy, is much lower than that of industrial robots.
Both service and industrial robots are mainly used in large enterprises; the manufacturing sector is leading the adoption of both types of robots. Only a small share of enterprises in other sectors are currently deploying robotic technologies.
There are numerous motivations for companies to invest in robotic applications. Eurostat data indicate that a significant share of enterprises prioritise internal factors such as productivity, safety and competitiveness as drivers of robot adoption. However, external labour market conditions, including high labour costs and challenges in personnel recruitment, also play a significant role, particularly in countries where these issues are prominent on the policy agenda.
Data suggest that the use of robots that interact with humans is associated with unfavourable working conditions, including heightened work intensity, reduced autonomy, increased surveillance and a higher prevalence of working alone. This emphasises the importance of preventing and managing psychosocial risks during the introduction and implementation of robotic technologies in workplaces.
6.3%
At EU level, the share of enterprises using robots experienced a slight decline between 2018 and 2022, from 6.7% to 6.3%. Europe continues to hold its position as the second-largest market for industrial robotic installations globally.
1 in 5
On average, around 1 in 5 large companies in the EU use industrial robots: e.g. robots used for welding, laser cutting or spray painting.
vs
1 in 10
On average, around 1 in 10 large companies in the EU use service robots: e.g. robots used for surveillance, cleaning or transport.
16%
Manufacturing is the main industry in which both industrial robots (16% of enterprises) and service robots (around 4%) are used.
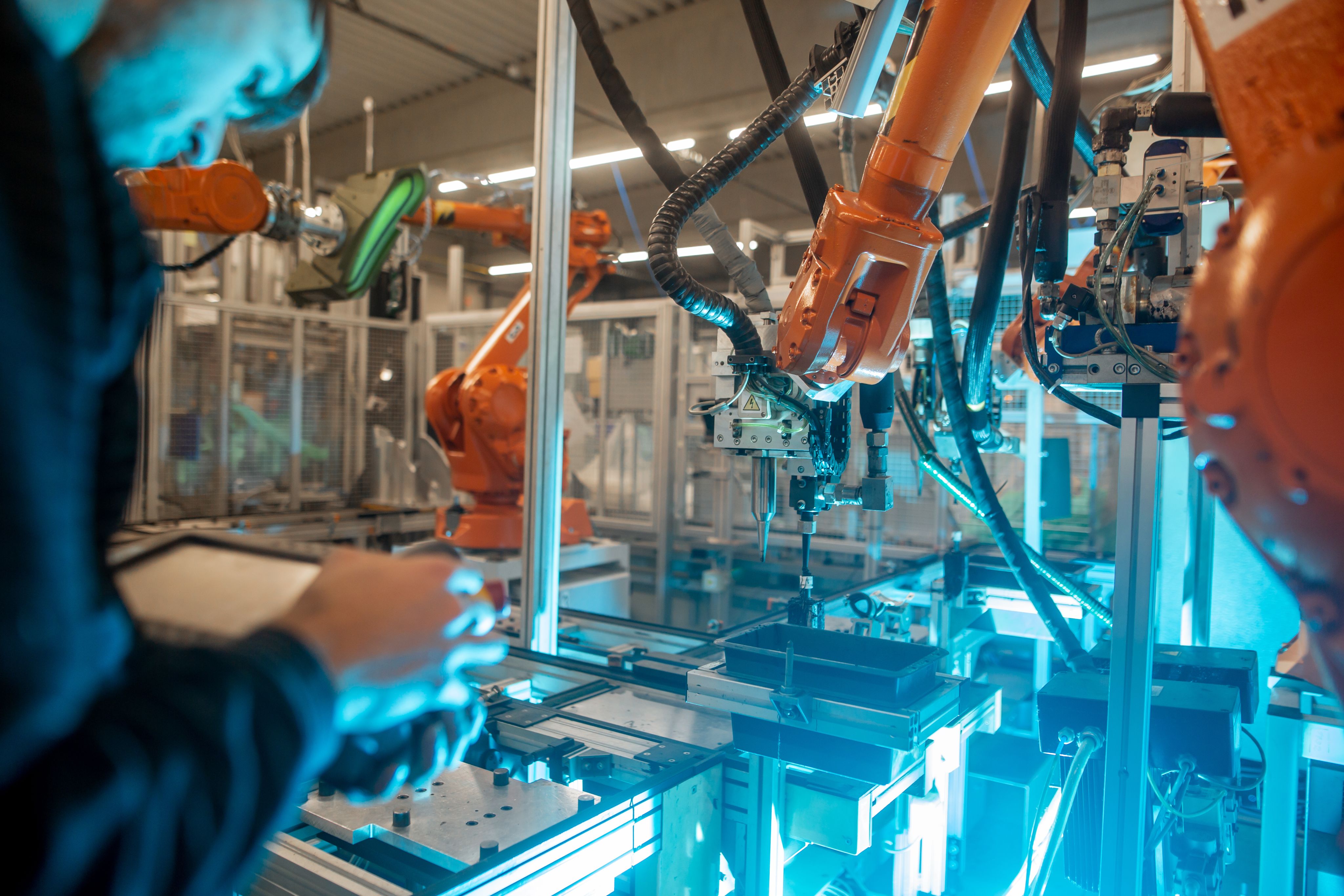
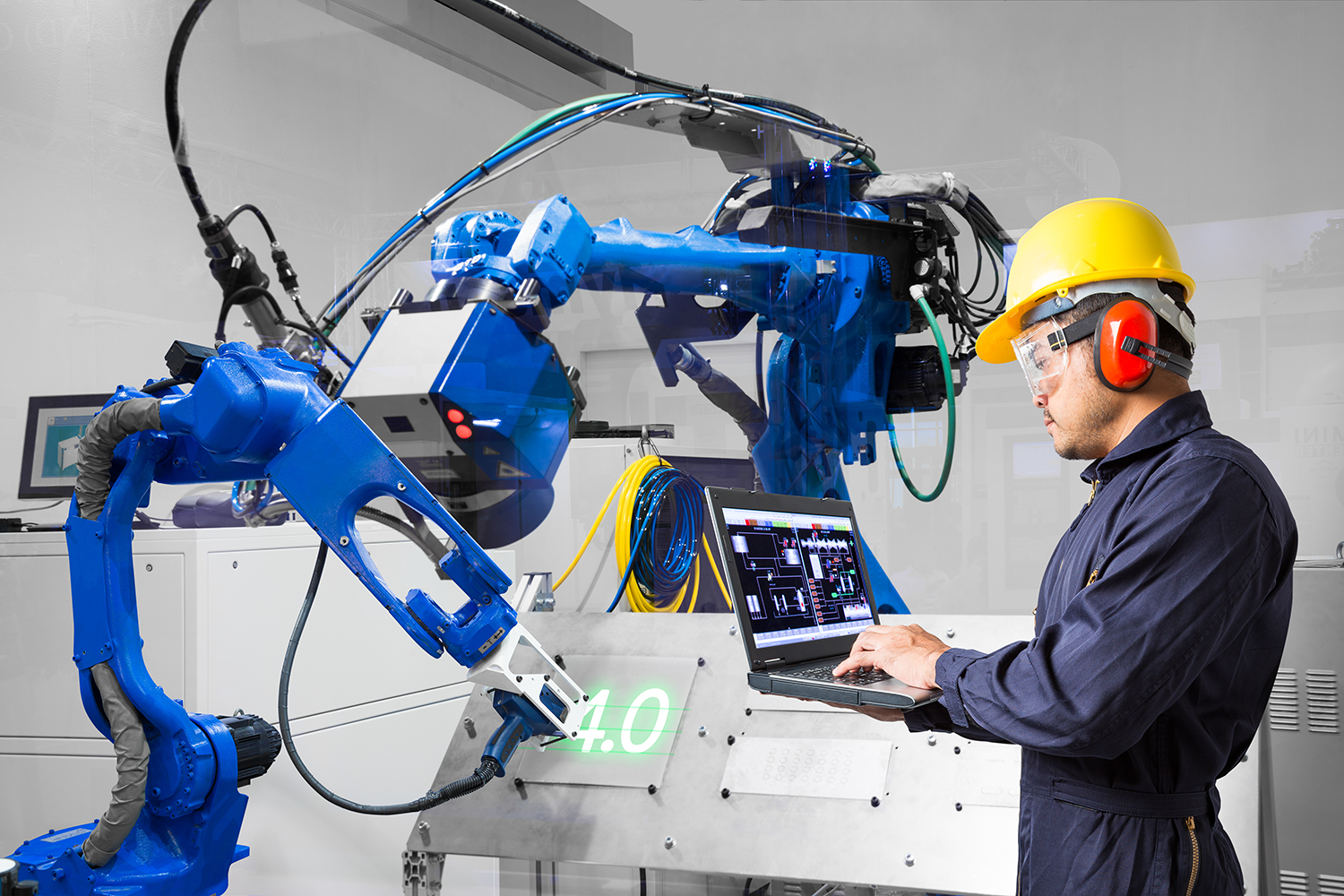
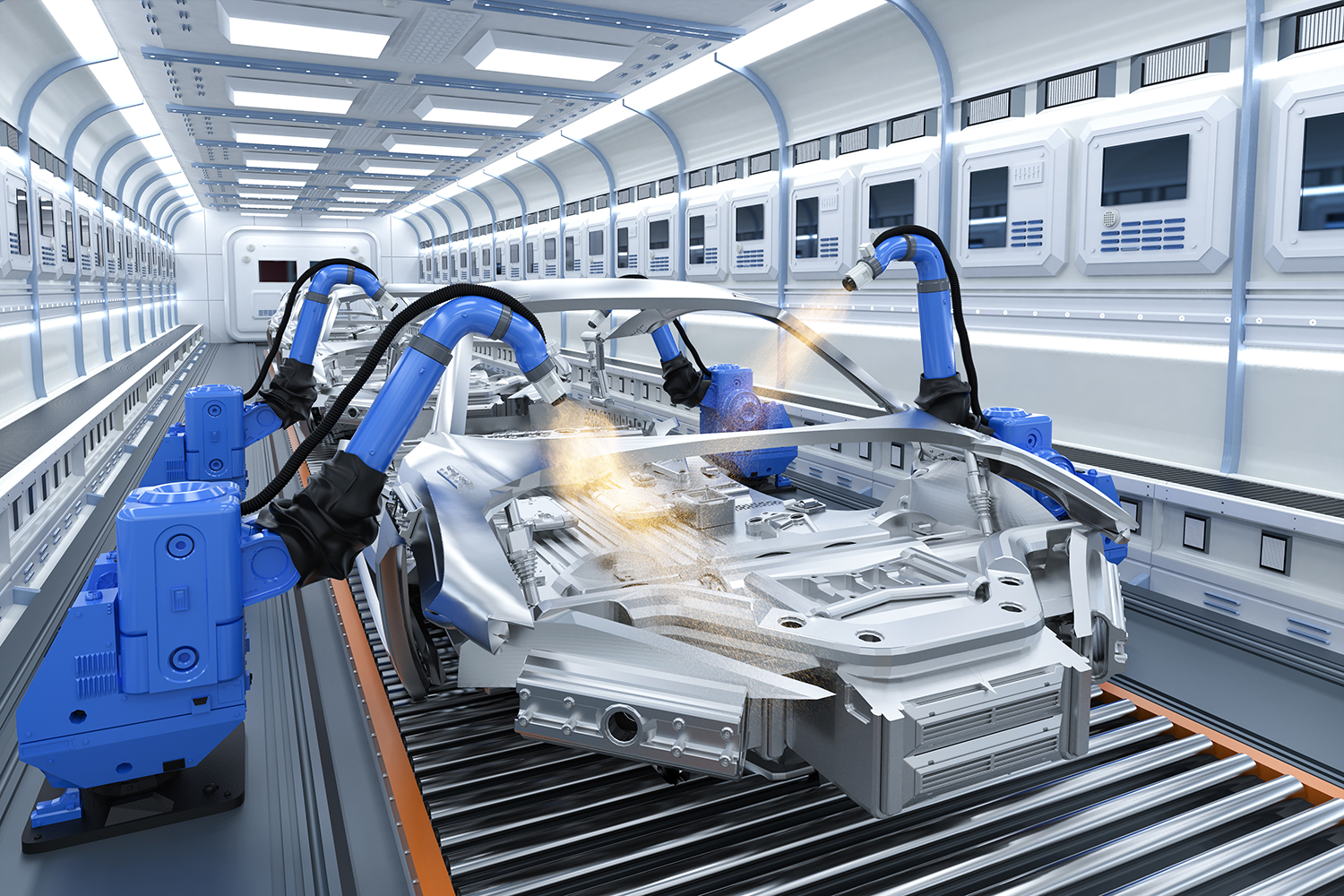
What are industrial robots?
Industrial robots can perform physical tasks and manipulate objects in a standardised way without having advanced capabilities for interaction. Industrial robots perform tasks in a structured environment with external safeguards. They are used primarily for automation in manufacturing.
Key advantages
- Automatically controlled, reprogrammable, multipurpose manipulator programmable on three or more axes
- Suitable for handling heavy and large materials and objects
- Can be fixed in place or mobile
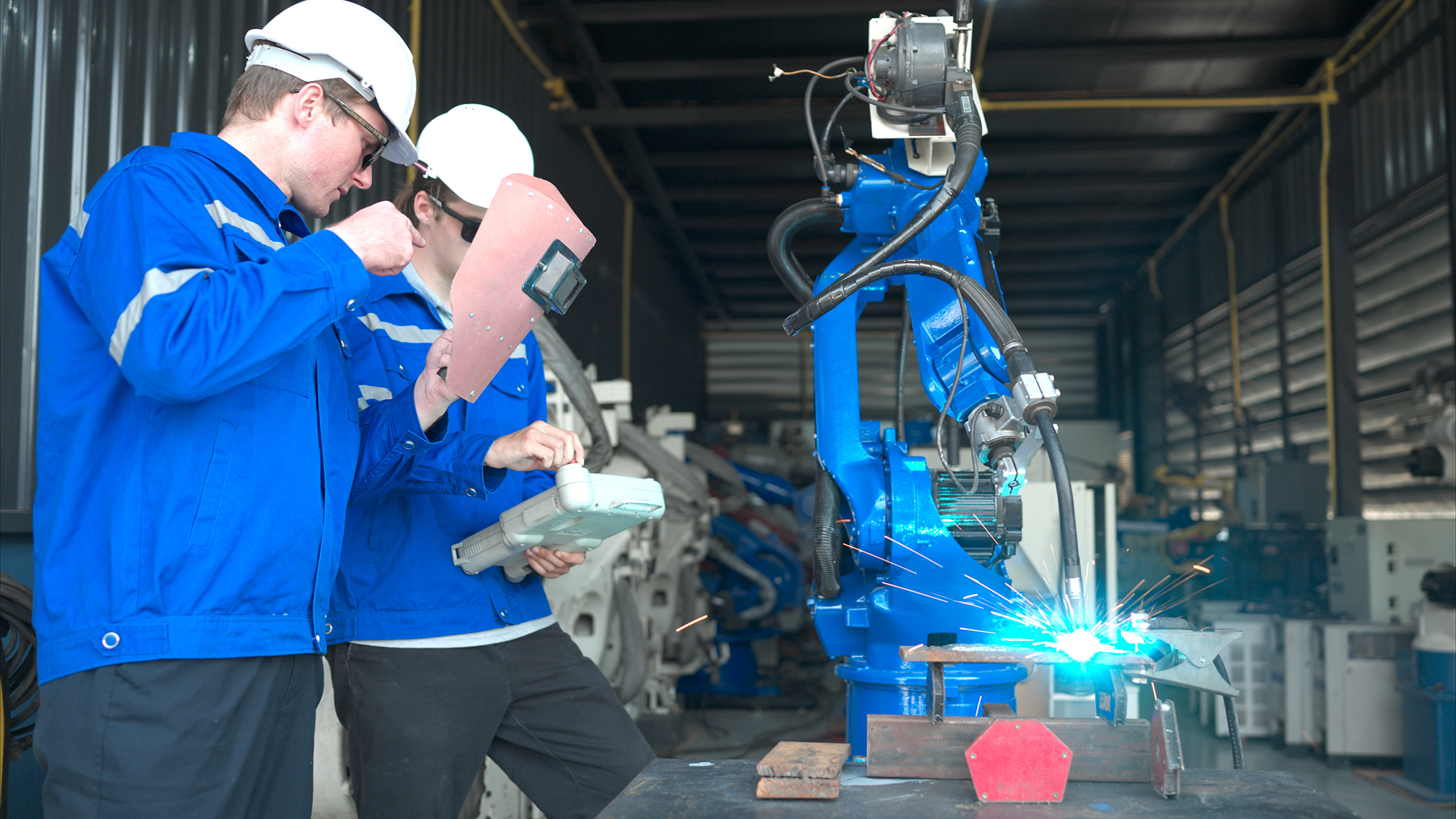
What are service robots?
Service robots have a degree of autonomy, which allows them to operate in human environments. As a result, they require greater sensing, motion and decision-making capabilities and are designed to perform specific tasks. The most common use of service robots (just over 40% in 2020) was in warehouse management systems, followed by cleaning or waste disposal tasks (around 29%).
Key advantages
- Adaptability
- Lower capital requirements than industrial robots
- Capable of executing more complex tasks than industrial robots
- Help to ensure high-precision outputs and processes
- Help to increase safety at work
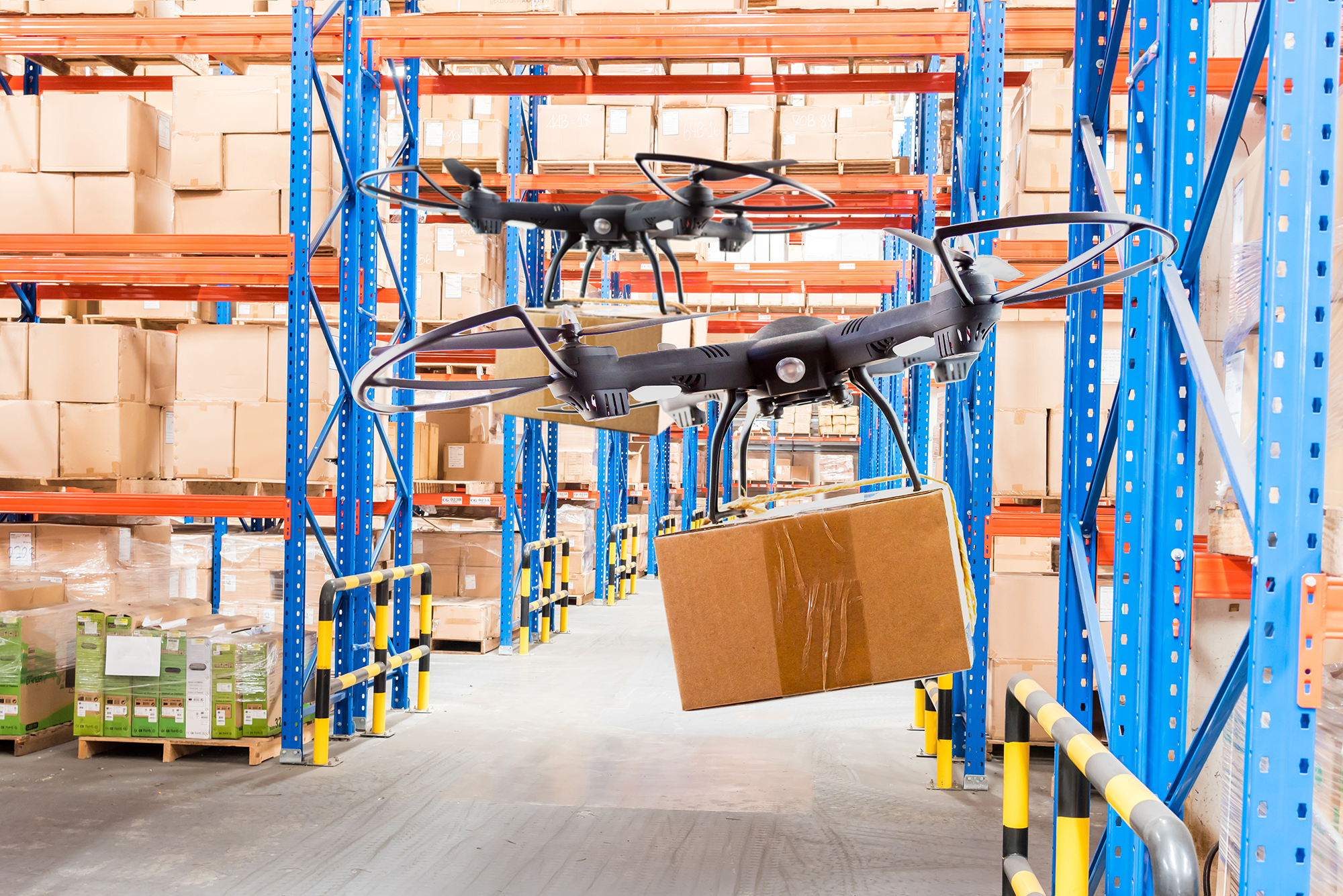
EU-OSHA’s OSH Pulse survey data suggest that the use of robots (that interact with humans) is associated with heightened work intensity, reduced autonomy, increased surveillance and a higher prevalence of working alone.
'Systematic monitoring of (new) human–robot collaborations is crucial for a thorough assessment of their impact on workers' well-being and productivity.'

Chapter 2
Advanced robotics and human factors in technology adoption
Summary
The adoption of robotic technologies is driven by various motivations, shaping human–robot interaction and influencing design choices and implementation. Efficiency and productivity gains were the main motivations for technology adoption in the establishments that were operating more complex robotic systems. Improvements to working conditions were highlighted as a secondary motivation in most case studies. Human centricity was not a primary consideration in the design of the robotic systems and applications investigated.
In line with findings from previous case study research on automation, risk assessments for robotic systems focused primarily on physical safety in most of the establishments investigated. In addition, they were often conducted on a one-off basis at the time of technology adoption, with limited consideration for other human factors in human–robot interaction. Safety testing and piloting, typically led by IT providers, generally lacked direct worker involvement. In cases where employees were more actively involved in risk assessments or piloting, the primary focus was on technical considerations rather than ensuring human-centric design. Gaining workers’ perspectives when introducing robots to workplaces is essential for enhancing human–robot interaction.
The case study evidence highlights a focus in training on ensuring the safe and correct use of robotic solutions, with more tailored training for specific roles. The training is often led by senior staff. Notably, training provision across establishments was not integrated into comprehensive change management programmes aimed at assisting workers in adapting to new roles and work practices resulting from increasing human–robot interaction.
Research on automation, and more broadly digitalisation, has consistently demonstrated that a participatory approach to technology adoption fosters trust and a sense of co-responsibility for safety and efficiency among workers, and increases their acceptance of the technology. In all cases investigated, the decisions to introduce the robotic technology were made by top-level management, without the active consultation or involvement of employees or their representatives.
Worker representatives generally viewed the technologies positively, stating that they increased workers’ safety and reduced physically demanding tasks. They therefore did not resist or object to the technology being adopted. The representatives played an important role in communicating workers’ concerns, particularly about potential future job displacement, to management. Most pressing concerns were most effectively addressed by line managers or HR managers with established relationships with workers built on mutual trust.
AGVs/AMRs
Besides cobots, other common robotic applications deployed in manufacturing are advanced guided vehicles (AGVs) and autonomous mobile robots (AMRs). These applications involve a more moderate level of human–robot interaction than cobots, with human involvement generally limited to monitoring, supervision, maintenance and exception handling.
Transport & warehousing
Interconnected robotic systems, like AGVs and AMRs, are transforming port terminals by optimising cargo handling and boosting container throughput. These technologies are also being integrated into mobile shelving solutions in warehouses, enhancing the efficiency of order fulfilment. This application exemplifies elements of algorithmic management whereby warehouse workers are closely directed as to what items to pick, move, store and ship, and how to do so. The robots are typically connected through software solutions for real-time monitoring, optimisation, scheduling and centralised control.
Manufacturing
Several manufacturing facilities, particularly automotive, employ AGVs and AMRs extensively to facilitate efficient material movement along assembly lines.
Construction
Construction is another sector where the prevalence of advanced robotics is expected to increase over time as technology continues to advance. Advanced robots hold the promise of improving efficiency, bolstering safety measures and mitigating labour shortages in the construction industry.
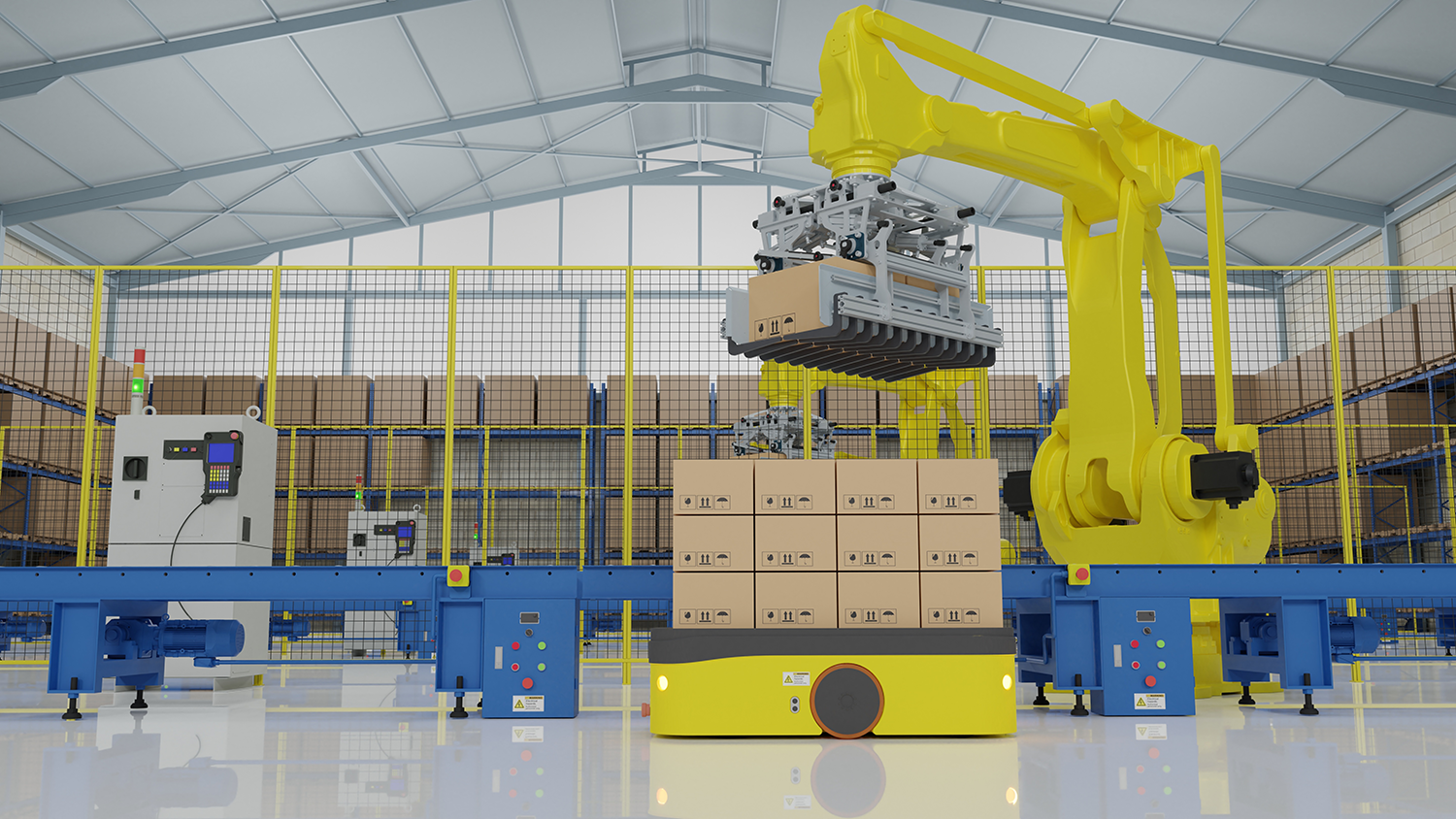
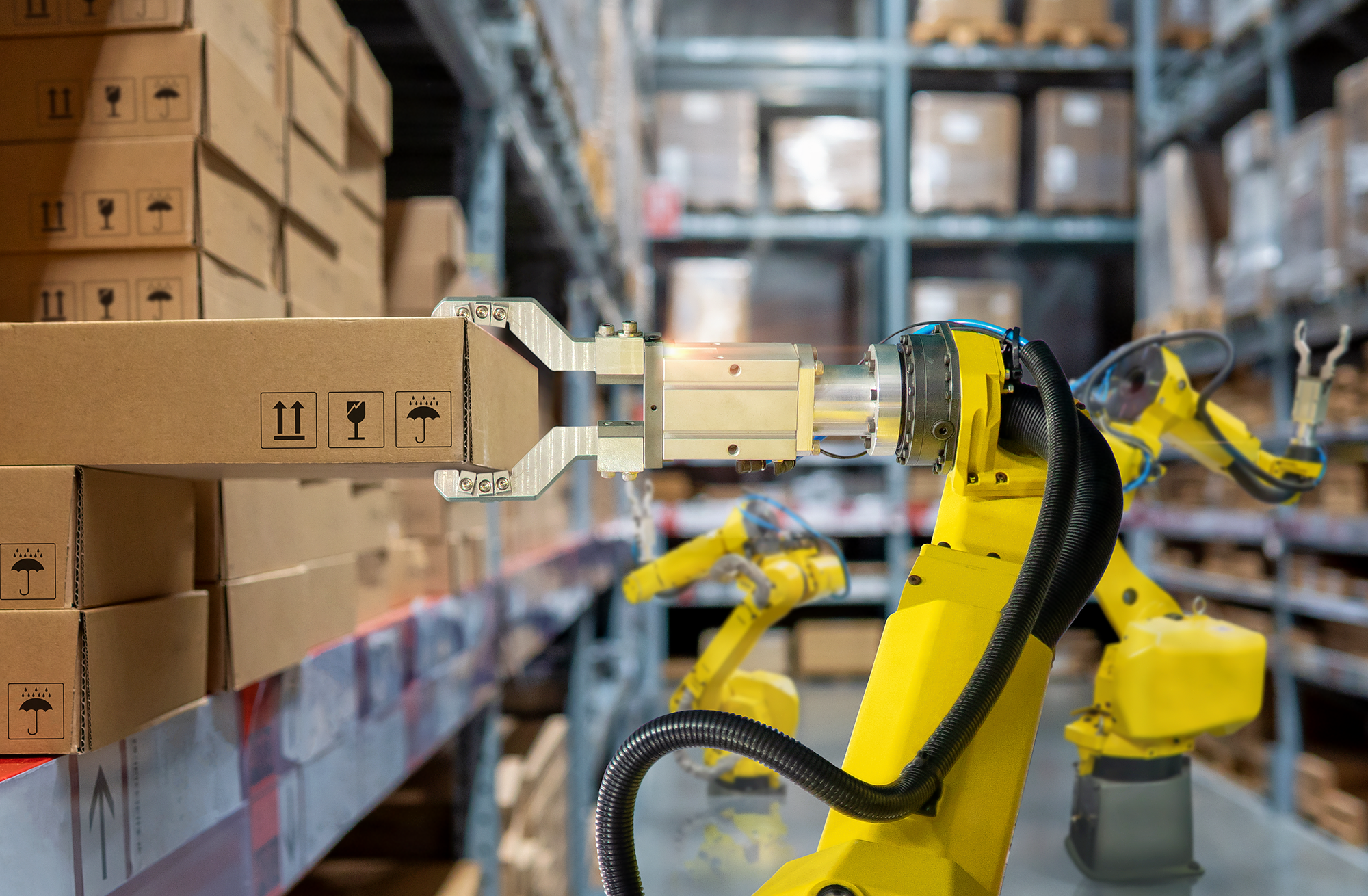
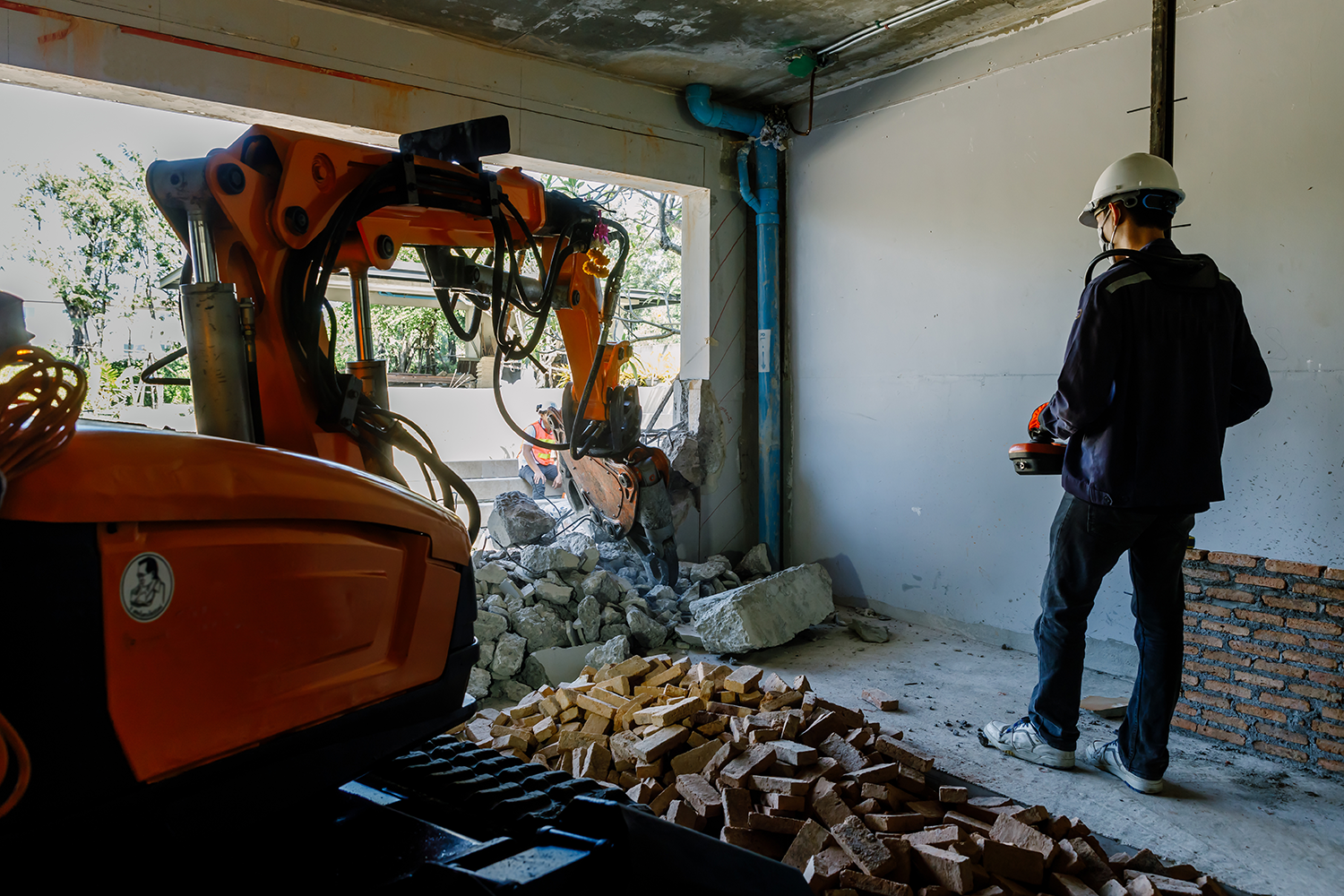
What are cobots?
Collaborative robots, or ‘cobots’, are robotic applications designed to work alongside humans in a shared workspace or in close proximity to humans, enhancing their capabilities and increasing productivity. Due to their versatility, cobots have various uses across different industries. They are mostly used in manufacturing, healthcare and support services (cleaning activities).
Key advantages
- Typically small and compact, low costs, lightweight design, high mobility, floor space savings, versatility
- Easy installation and programming
- Relieve workers from tedious, repetitive or physically demanding tasks
- Can increase the efficiency and accuracy with which tasks are completed
- Equipped with advanced safety features and sensing technologies to ensure safe human–robot interaction
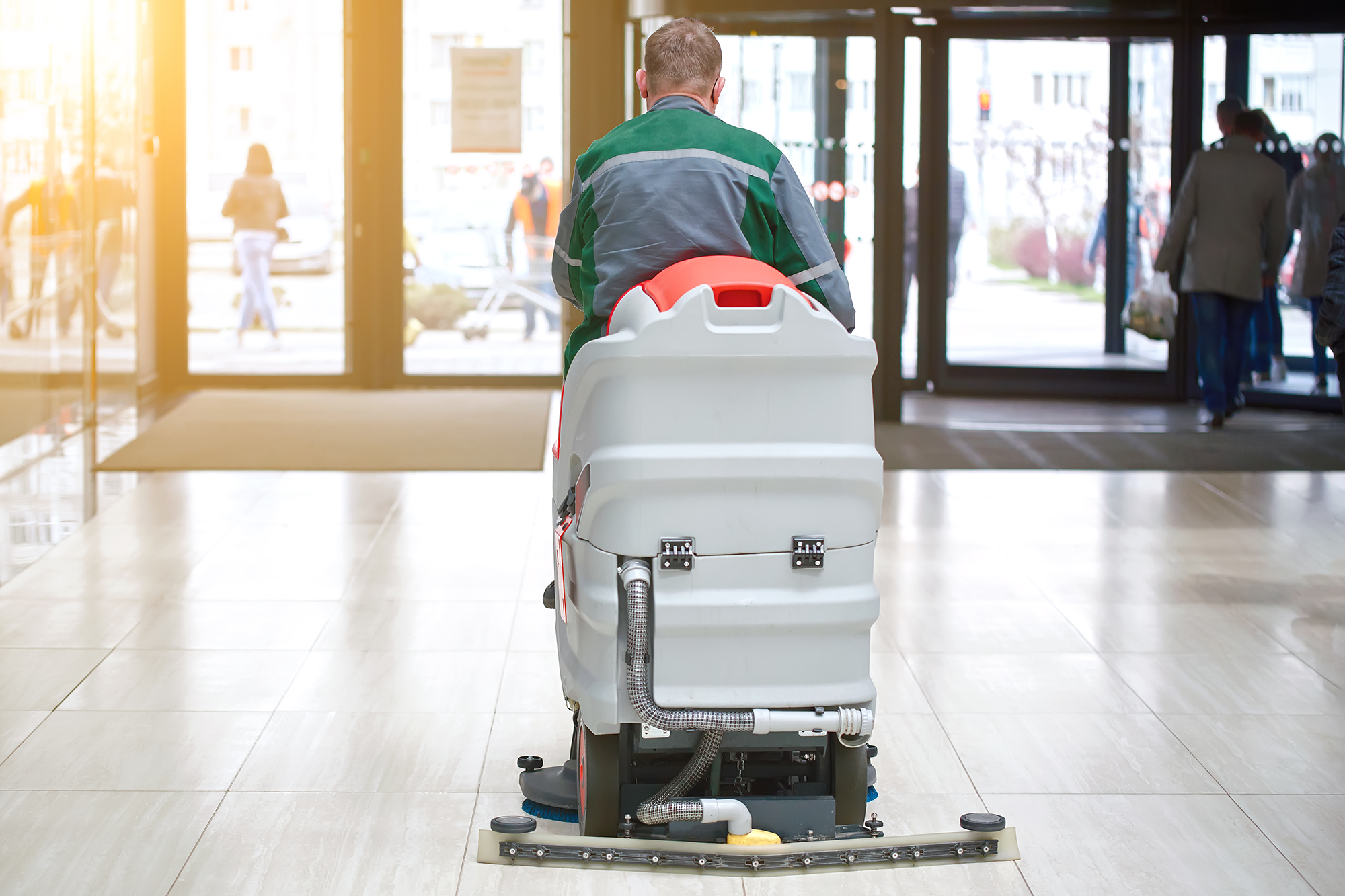
What are social robots?
Social robots are autonomous robots designed to interact and communicate with humans socially. They are equipped with sensors, actuators and advanced AI algorithms, enabling them to perceive their environment, process information and respond to human cues and commands. Social robots are gaining traction in the services sector, notably in retail, healthcare, entertainment and education.
Key advantages
- Integrated AI capabilities
- Can offer personalised customer experiences
- Can help to increase staff productivity
- Helps to alleviate some of the physical workload
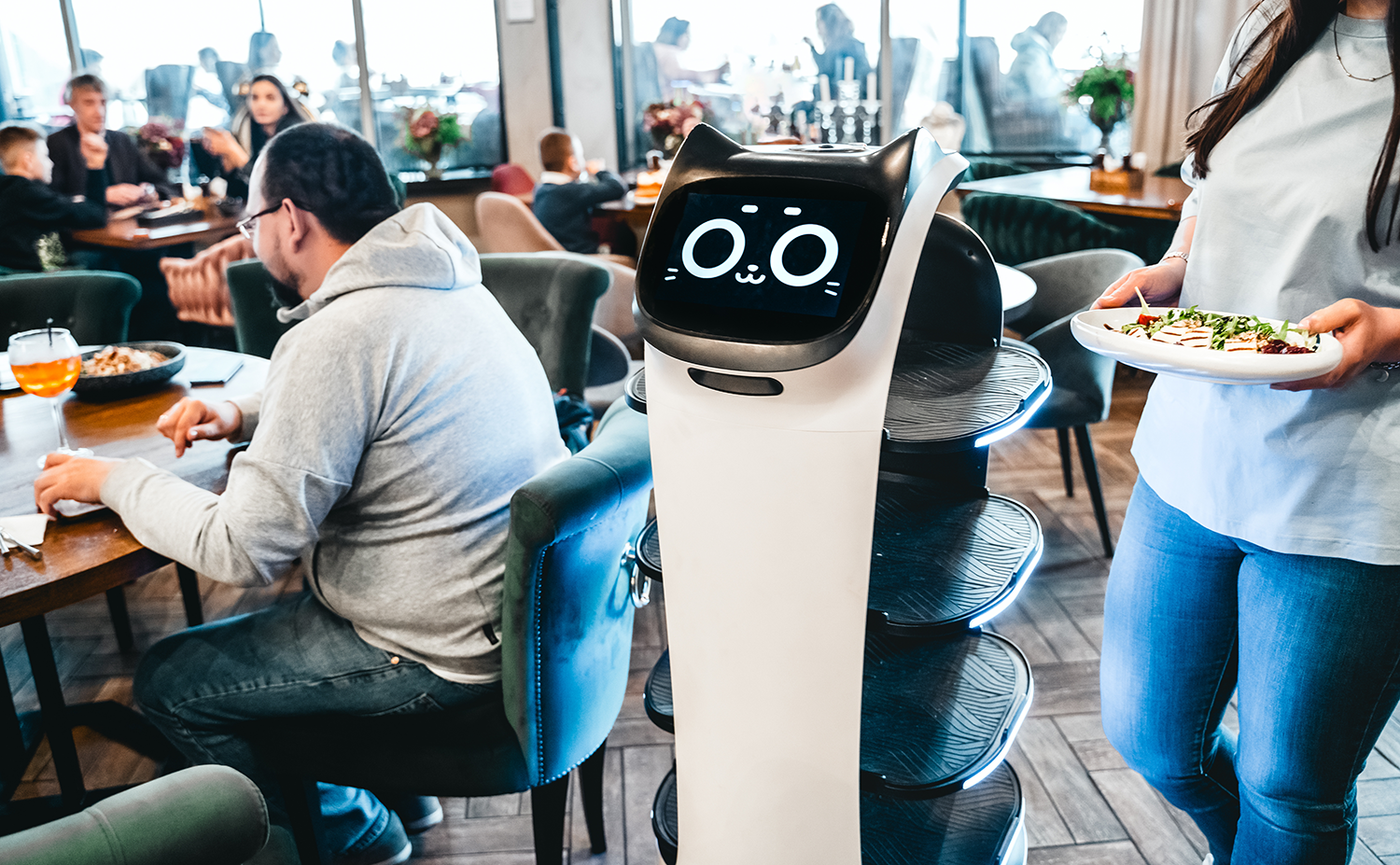
'It is not enough to train workers to use robotic equipment safely. Upskilling, akin to change management, plays a central role in fostering workers’ adaptability in the face of constant change.'
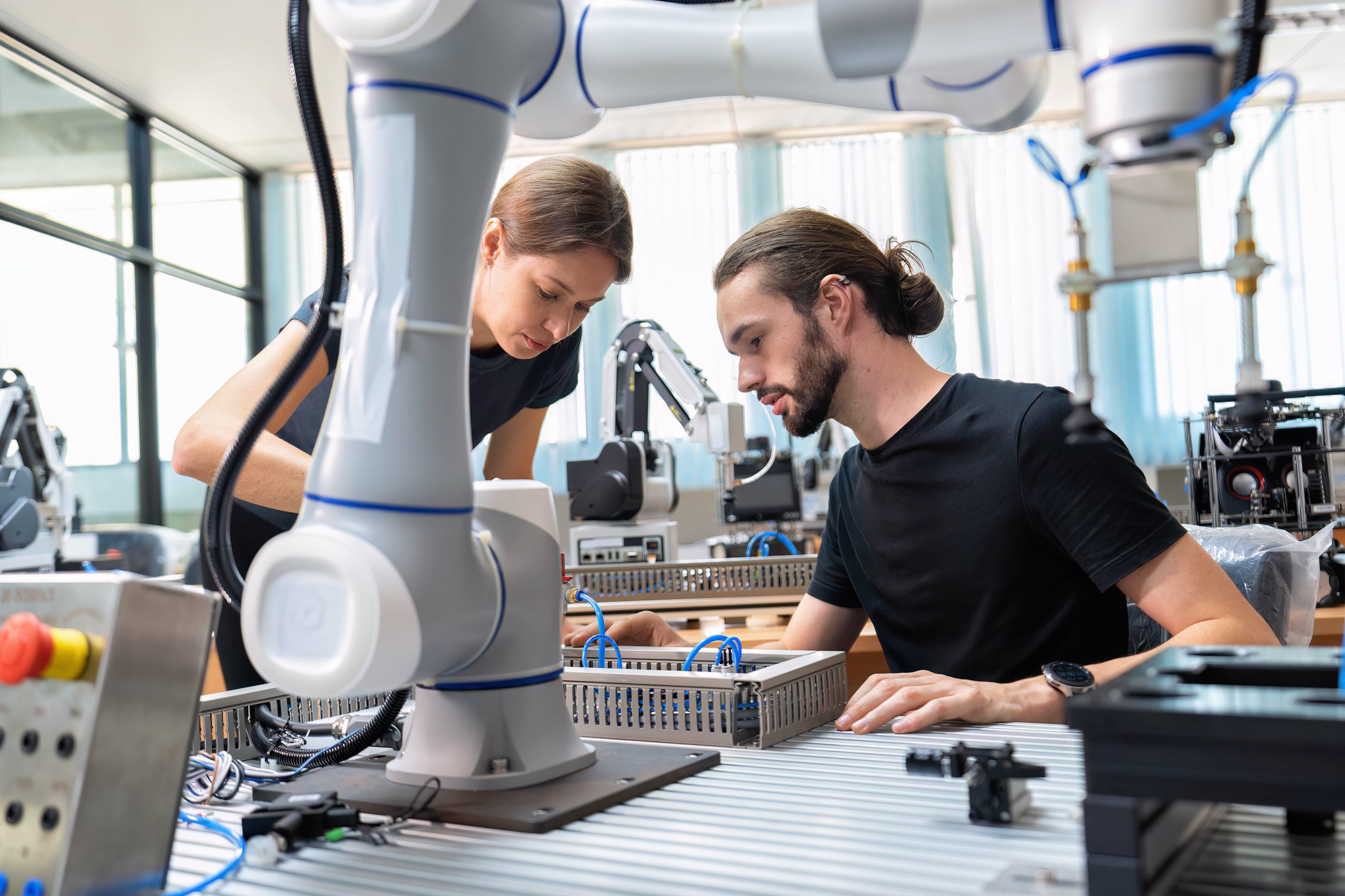
Chapter 3
Impact on work organisation and working conditions
Summary
The adoption of robotic technologies in the establishments investigated resulted primarily in the automation of manual and routine tasks, and did not affect entire job profiles. The most significant changes to the nature of tasks were observed in establishments that adopted more complex and interconnected robotic systems.
In establishments with complex robotic systems, the adoption of the technology necessitated the redesign of the workspace and substantial adjustments to existing workflows, with a primary focus on safety and ergonomic considerations. In these establishments, the robotic systems rely on the real-time collection and processing of large amounts of data about workers’ activities. Although it is technically feasible, the managers interviewed denied monitoring the performance of individual workers. Monitoring is typically carried out at the level of the team or production line, or the establishment.
With close human–robot interaction and in highly standardised work environments, robotic systems may further restrict their operators’ freedom to determine how to perform their jobs. In cases where the robotic technology is a discretionary tool for staff, which complements their work, no changes to job discretion were observed.
No evidence of deskilling was found in the establishments investigated; if anything, workers operating or using robotic systems reported an improvement in their digital competencies and skills, primarily acquired on the job rather than through formal training.
The implementation of robotic technologies in the establishments investigated did not result in changes to working hours; instead, the time saved was redirected towards handling an increased number of orders or allocated to value-added tasks. Work intensity varied across establishments and was often determined by management decisions or the suboptimal organisation of work, rather than the technology itself.
The case studies point to diverse impacts of robotic solutions on the social environment. Some robotic systems – such as those implemented in warehouses – tend to restrict social interaction. However, the positivity or negativity of the impact is contingent on specific applications, and, crucially, on design and management decisions.
The advanced robotic systems and applications examined were designed with embedded safety precautions and ergonomic considerations. Overall, they had a positive impact on the physical environment, by performing tasks that are repetitive or physically demanding for workers, thereby reducing physical strain and lowering the risk of injuries or accidents. Some robotic solutions were also intended to streamline and simplify tasks and in doing so reduce workers’ mental load. However, in some instances, mental load increased due to additional demands on workers operating the advanced equipment.
With regard to earnings and career prospects, the increased productivity and efficiency resulting from technology adoption across all establishments investigated did not translate into salary increases or tangible career advancement for affected workers.
There is no evidence of redundancies resulting from technological change in the establishments investigated, nor are there examples of entirely new occupations being created due to the introduction of the new robotic systems or applications. However, concerns about future job losses persist among workers in some of the establishments investigated. Despite management’s assurances, companies’ plans suggest a trend towards increased automation, potentially leading to redundancies in the not-too-distant future.
Workplace redesign
Ergonomic considerations were identified as fundamental elements of the workplace design process. An important requirement for such systems was to improve overall ergonomic working conditions, by opting for a design that minimised the physical workload for the operators.
Job tasks
Automation of repetitive and monotonous tasks by robotic systems and applications in the selected establishments studied led to the transformation of job routines for workers. This transformation resulted in increased task variety and a shift towards more problem-solving-oriented tasks, demonstrating clear potential for enriching the overall content of work.
Monitoring and control
In Industry 4.0 work environments, the capture of human data (either directly or indirectly) and monitoring of workers' activities through digital devices and sensor technologies is inevitable, often occurring as a by-product of production processes. In the establishments investigated, future plans invariably involve scaling up the technology, often leveraging AI capabilities. This may give rise to more data-centric management and control practices.
Job discretion
The high level of standardisation required in automated work environments further restricts workers' discretion over tasks and methods when operating robotic systems. Job discretion was unaffected only in establishments where the use of robotic applications was optional for workers.
Skills use and requirements
In most of the establishments investigated, the interfaces were generally considered user-friendly and only demanded basic digital skills. However, given the extent and variety of demands on staff interacting closely with robotic systems and applications, workers should upskill and engage in lifelong learning throughout their entire professional careers.
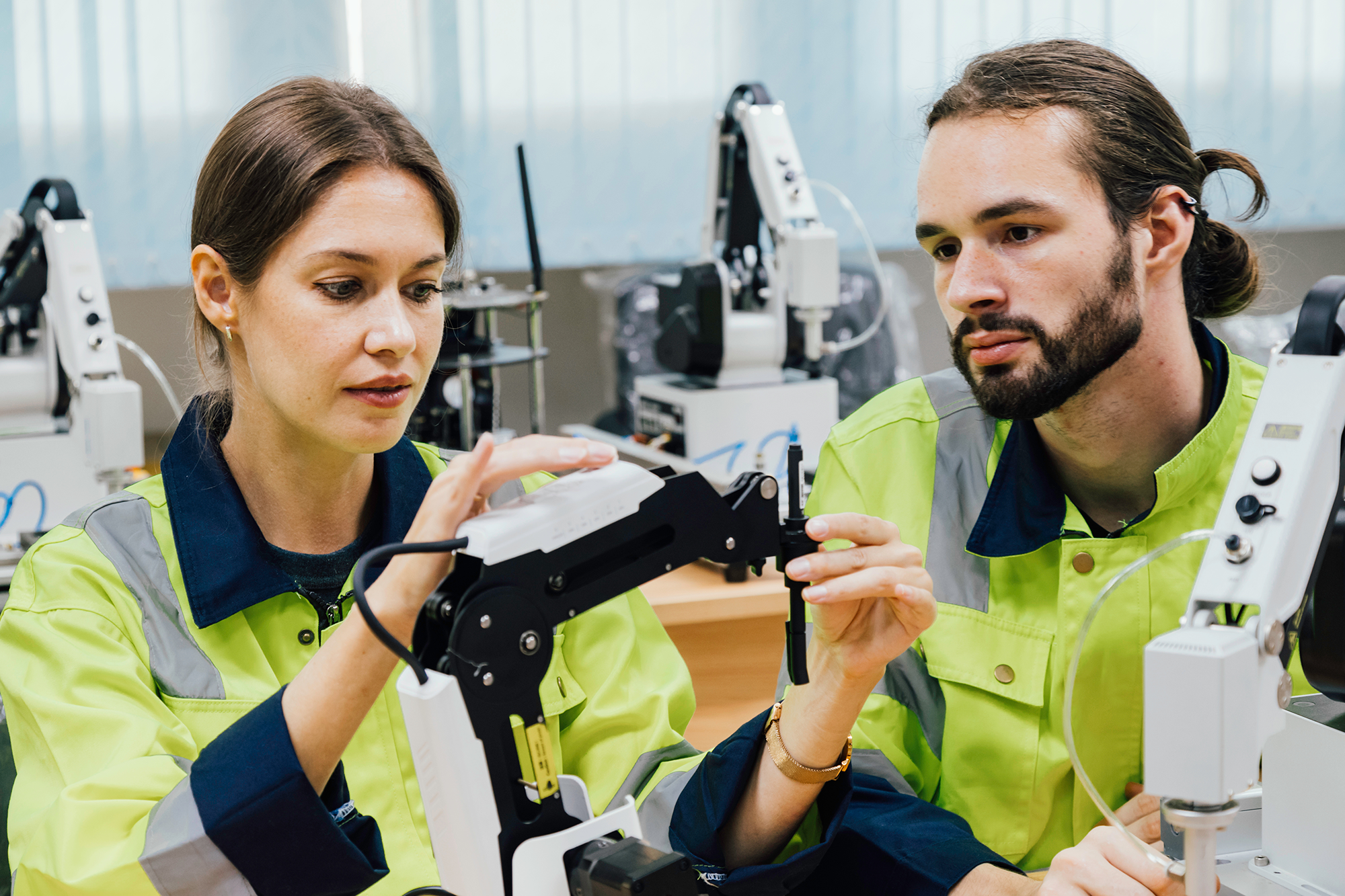
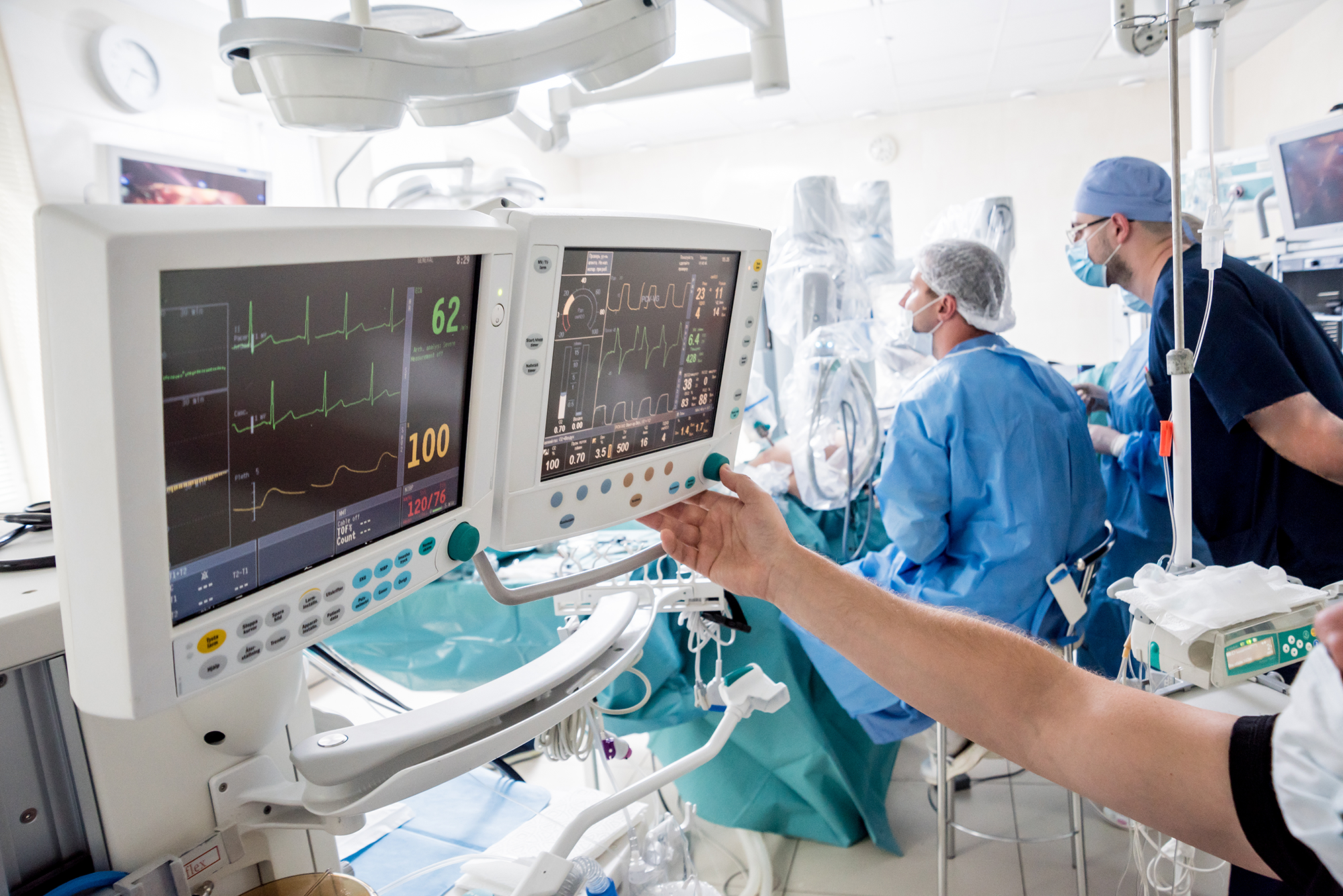
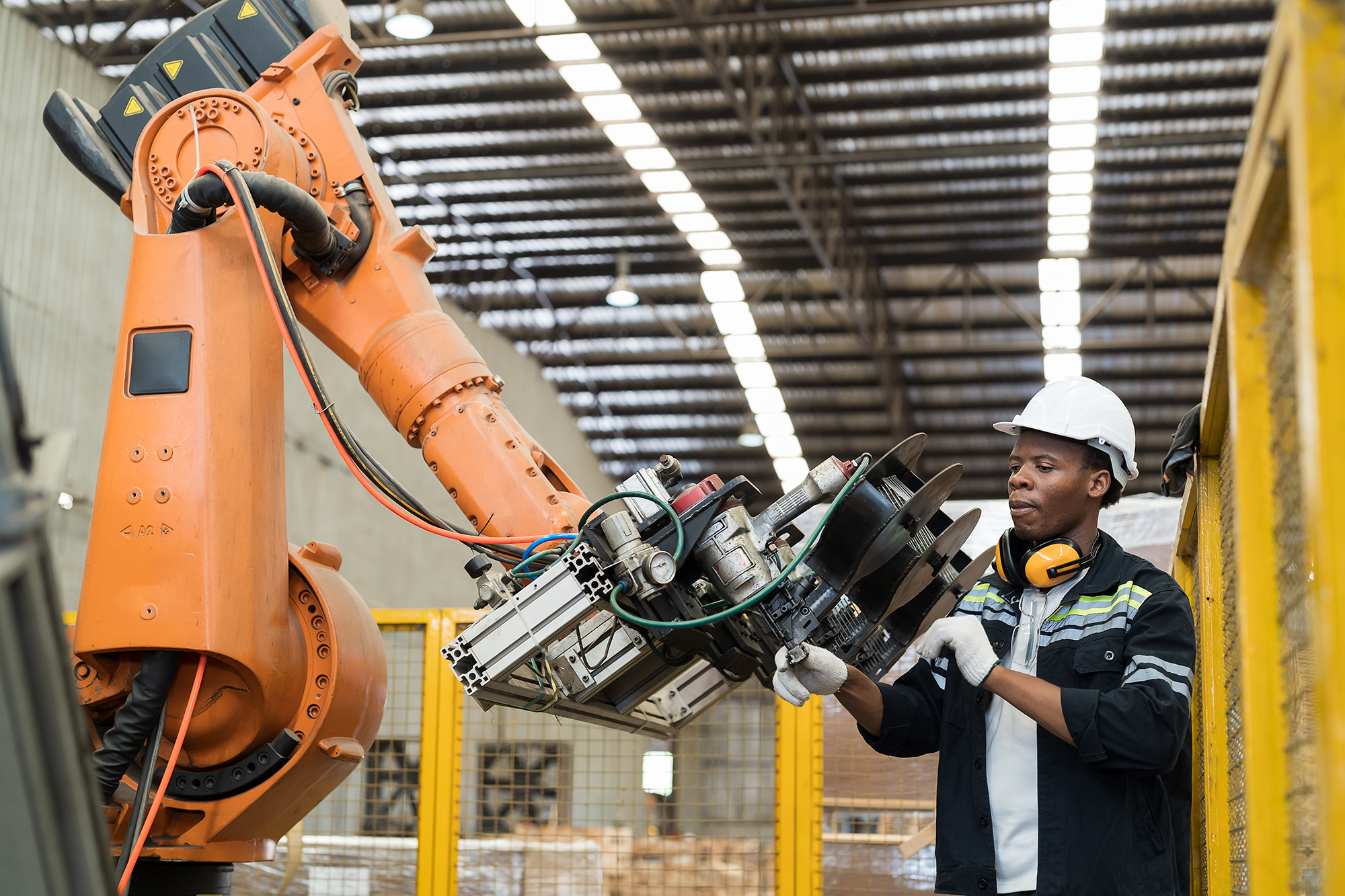
'The success of implementing advanced collaborative robotic systems hinges on the careful consideration of how and which tasks are (re)allocated to humans.'

Policy pointers
Robotic technologies, particularly when AI-powered, promise to boost productivity, increase workplace safety, alleviate task monotony, reduce physical strain and make work more engaging and rewarding. However, realising these advantages necessitates treating workers as co-creators of technological solutions, rather than merely costs to be minimised.
Policy actions are essential to promote human-centric design, including awareness-raising campaigns, public incentives for research and development with a focus on human centricity, and the development of guidelines for ethical and human-centric design.
The social partners can play a crucial role in shaping policies that prioritise human-centric values and involve participatory approaches to technology design and implementation in workplaces. The European social partners’ 2020 framework agreement on digitalisation is an important instrument for coordinating efforts and promoting human centricity in relation to robotics.
Continued efforts should be directed towards supporting training initiatives that prioritise the development of skills relevant to human–robot collaboration, including digital literacy and adaptability and resilience in the face of automation.
It is equally essential to ensure the effective implementation of principle 10 of the European Pillar of Social Rights (on health and safety) and the EU strategic framework on OSH. The new EU strategic framework on OSH for 2021–2027 underscores the importance of anticipating and managing change in the new and increasingly digital world of work, putting a renewed emphasis on the need to tackle risks to psychosocial well-being.
An unresolved issue is the extent to which productivity gains from automation should or could be shared in an equitable way with workers. It may be necessary to rethink what productivity means in the digital age and develop new approaches and metrics to fully capture the changes in productivity.
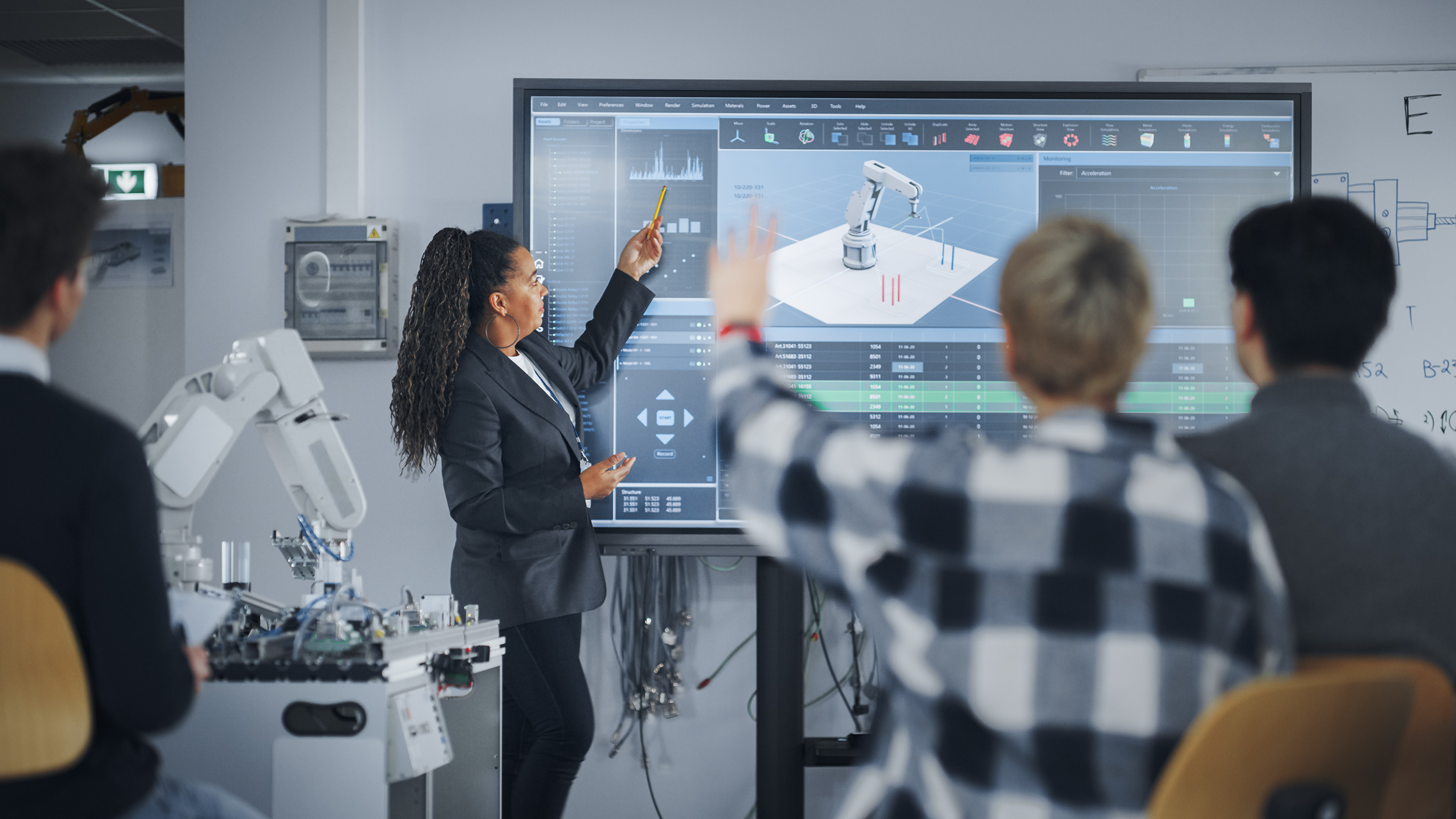
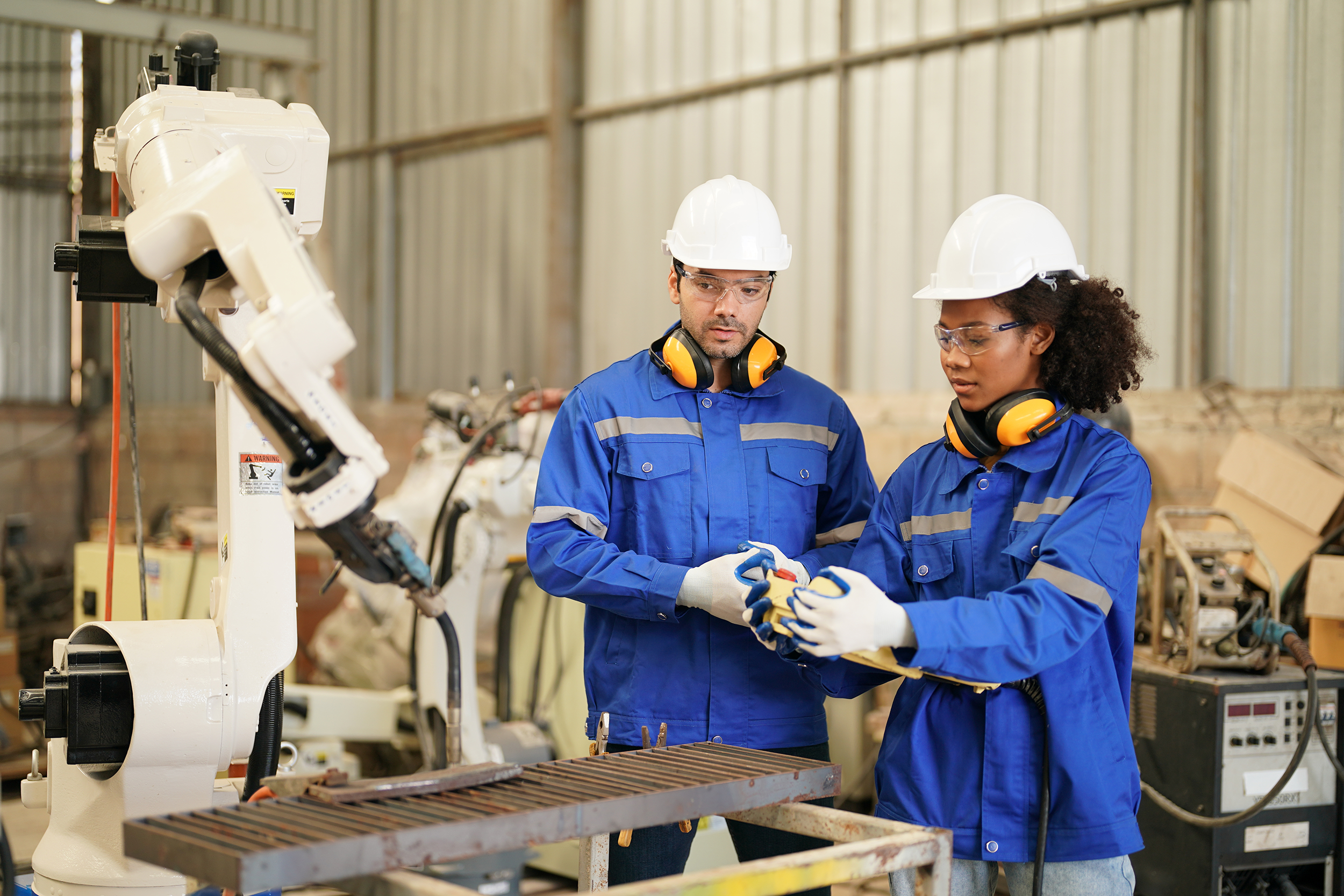
Read the full report
Key messages and executive summary available in 21 EU languages
Authors
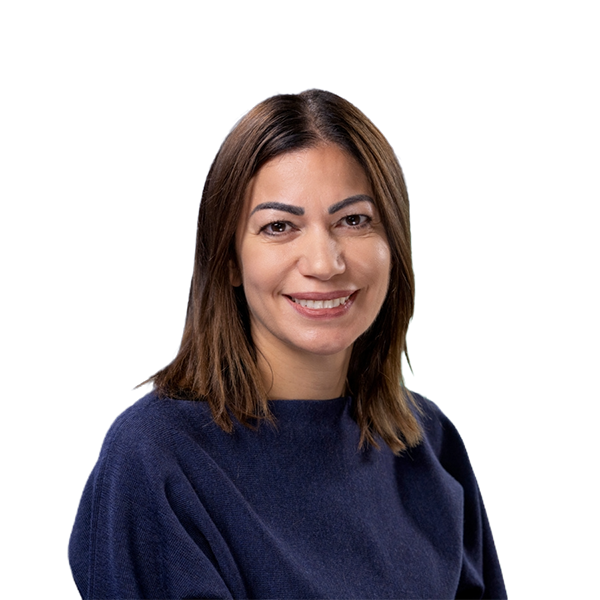
Sara Riso
Sara Riso is a research manager in the Working Life unit at Eurofound. She is involved in research projects in the areas of employment change and restructuring.
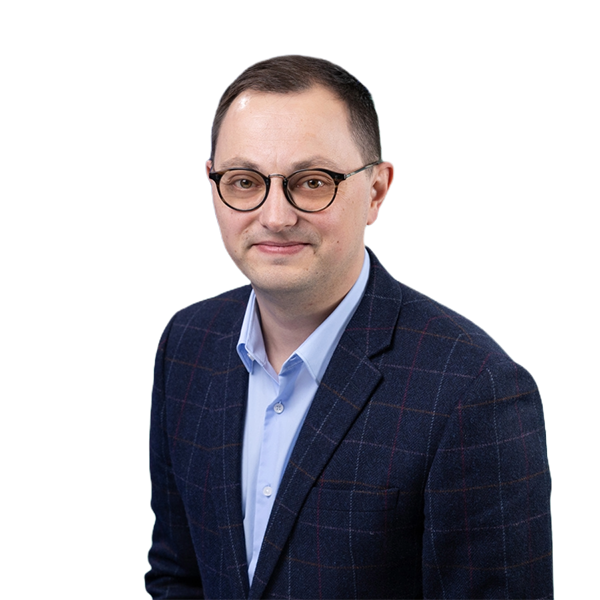
Dragoș Adăscăliței
Dragoș Adăscăliței is a research officer in the Employment unit at Eurofound. His current research focuses on topics related to the future of work, including the impact of artificial intelligence on jobs, the consequences of automation for employment and regulatory issues surrounding the platform economy.
Photo credits (in order of appearance)
Title: © greenbutterfly/Adobe Stock
Key messages: © Montri/Adobe Stock
Chapter 1: 1: © Khaligo/Adobe Stock; 2: © kinwun/Adobe Stock; 3. © phonlamaiphoto/Adobe Stock; 4: Industrial robot © Wosunan/Adobe Stock; 5: Service robot © Voy_ager/Adobe Stock 6. © kelvn/Adobe Stock
Chapter 2: Chapter 2: 1: © Nay/Adobe Stock; 2: © Pugun & Photo Studio/Adobe Stock; 3: © Ekkasit A Siam/Adobe Stock; 4: Cleaning robot © Tricky Shark/Adobe Stock; 5: Social robot: © velirina/Adobe Stock; 6: © Tongpool/Adobe Stock
Chapter 3: 1: © gumpapa/Adobe Stock; 2: © romaset/Adobe Stock; 3: © amorn/Adobe Stock; 4: © Gorodenkoff/Adobe Stock
Policy pointers: 1: © Gorodenkoff/Adobe Stock; 2: © FotoArtist/Adobe Stock